Online CPR Certification Blog
What’s an Exposure Control Plan & Why You May Need One in Your Workplace?
Date: February 15th, 2020
Implementing an Effective Exposure Control Plan
Does your workplace have an exposure control plan (ECP)?
If it doesn’t then you should asses your risk levels and determine if you need to implement one.
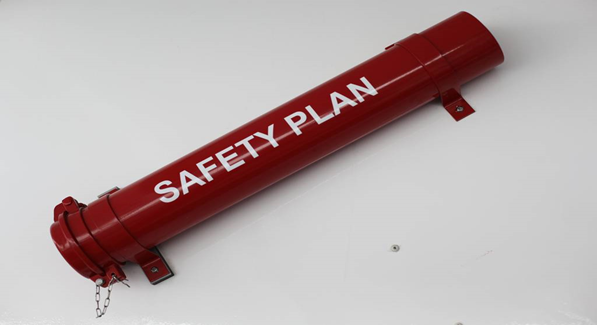
But for most industries, OSHA Bloodborne Pathogen Standard requires that employers develop an exposure mitigation strategy. This law expects a well-documented plan with clear explanations on how you plan to control bloodborne pathogens exposure including a clear course of action.
The Critical Role of an Exposure Control Strategy
To start with, a control strategy protects your employees from contact with bloodborne pathogens.
Number two, it is a requirement by the law and you want to be in compliance more so if your staff are at the danger of bloodborne pathogens exposure.
And lastly, it saves you a lot of costs on compensating exposure cases, hospital bills, lost worker time and new hires by increasing awareness and reducing instances of infection.
So how can you execute an exposure mitigation plan in 10 steps?
- Inform your team about this plan using internal awareness campaigns. Display a copy of this document somewhere and let everyone know where it is located.
- Assign one employee with knowledge in Bloodborne pathogens and risk management to lead the plan.
- Determine all the job positions or company processes that expose employees to potentially infectious materials.
- Offer your workforce safety gadgets built to reduce all sorts of sharps injuries to workers who utilize these tools.
- Gather feedback from employees in the assessment and choice of safety gadgets. Include the safety device selection process in you official plan.
- Give the details of you course of action. Your exposure control plan should include the specific problem; how you plan to reduce control it and who is going to accomplish those duties.
- Mention the significance of personal protective equipment also known as PPE. Your official document must provide instructions on proper usage and use cases of the various PPEs, such as throwaway gloves, cut-resistant gloves, and face goggles for eye safety.
- Control the spread of hepatitis B protection by administering the vaccine free of charge to staffs. In your plan, include the people who will supervise the vaccine program and attach a form for staffs who decline your vaccine programs.
- Teach you workers on how to report any infection cases and develop a strategy for instant medical diagnosis and action. The best interventions also include psychological therapy.
- Bring up to date your Bloodborne pathogen ECP annually or during high-infection seasons.
Assessing Exposure Risks Accurately Can Lead to a Better ECP
You cannot draft an accurate exposure plan if you don’t assess workplace risks accurately.
Workplace risk assessment primarily aims at preventing potential dangers of exposure at a given workplace. Thus, it should always be done before executing tasks or activities in an organization and throughout the lifetime of a company.
In this case you will be assessing injury risks because workplace injuries are the main cause of Bloodborne pathogens exposure. So if you analyze your workstation risks accurately then you can draft an exposure control plan that covers all risks and protects your workforce.
Carrying out risk assessments before executing tasks or activities in the workplace ensures potential hazards are identified, eliminated or managed to low levels to avoid harm to the immediate persons.
It’s important to carry out risk assessments before significant changes are incorporated to existing activities. For instance, when there is change in equipment, machinery or new info on potential hazards within the workplace.
When you are doing an assessment, it’s important to consider the following factors;
- Take into account the technicalities in the workplace; for example processing procedures, handling of different tools and how to store these safely.
- How long an activity or a task takes to be done. Long daunting tasks can lead to staff burnout and increase the chances of an injury
- Locations where tasks and activities are executed. Is your workstation safe or does it expose workers to accidents?
- The educational background of all the workers. Do they have Bloodborne pathogen knowledge and training?
- Get a record of all activities within the workplace and whether they would affect others.
- The number of workers who might be exposed, the kind of exposure and how the exposure might happen.
- The measures and control procedures in place meant to reduce such exposure,
- The type of equipment, machinery and tools used in the workplace. Also, take into account how they are used and the kind of operation they execute.
These factors change from time to time; they should not only focus on the current state of the business or workplace. Instead, they should change as things changes
Considering these factors can ensure you carry out a complete workplace risk assessment.
The Fundamentals of an ECP: The Must-haves of an Effective Plan
Two years ago the CDC released the findings of a workplace bloodborne awareness research and what came out was that some US medical workers do not receive enough training enough or protection from infectious pathogens.
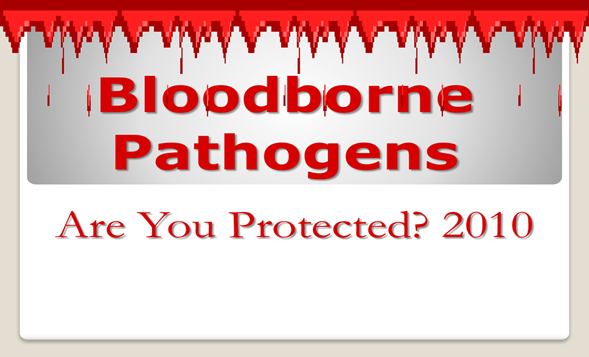
An entire 30% of private dental care service providers had not implemented a documented exposure control plan and 14percent of these foot draggers had not prioritized an intervention strategy in the coming year.
The Occupational Safety and Health Administration’s has provisions for bloodborne pathogens established to protect US workers from infections that spread from one person to the next through body fluids, and these regulations require that employers develop an exposure alleviation strategy to safeguard you staffs.
This official document is the basis for compliance as it allows an organization to develop and put on paper a plan to safeguard employees from bloodborne pathogens.
Operating without an ECP leaves your dedicated workforce exposed to any infectious pathogens. Plus, it means you are acting against Federal laws and a court may find you out of compliance.
That said, let’s discuss 7 must-haves of an ECP.
1. Exposure risk profile – This doc contains an analysis of the risks of pathogen infections. Determine all the job positions or company processes that expose employees to potentially infectious materials.
2. Execution and Control Procedures – Give the details of you course of action. Your plan should include the specific problem; how you plan to control it and who is going to accomplish those duties.
Use the following strategies to reduce the chances of pathogen exposure;
- An ECP – A documented plan explaining every course of action meant to help prevent and deal with potential pathogen exposure and train staff.
- Rethinking work processes and safety initiatives- Doing away with sharps by adopting equipment that reduce cases of cuts and lacerations. It also involves continuous creation of awareness about Bloodborne pathogens.
- Personal protective equipment (PPE) – Provide PPEs and insist on the significance of personal protective equipment. Your official document must provide instructions on proper usage and use cases of the various PPEs, such as throwaway gloves, cut-resistant gloves, and face goggles for eye safety.
- Workplace housekeeping- Explains the correct and safe procedures to operate, clean, and get rid of the different types of potentially infectious materials within the workplace.
- Labelling – All storage zones with potentially infectious materials must be labelled with visible warnings and danger signs to control the spread of infections. Use labelled waste bags to warn your employees. NB; labelling is also a requirement by OSHA so you may be found out of compliance for failing to label.
Here are other guidelines by the Occupational Safety and Health Administration (OSHA) to restrict needlesticks and sharps injuries that are known to lead to pathogen exposure:
- Keep off using needles and sharps in cases where there exist efficient needleless designs or the availability of Sharps built with safety in mind.
- No recapping of needles after use.
- Strategize about secure management and discarding of sharps and needles before implementing a technique that calls for use of sharps.
- Instantly discard utilized needles, needleless designs, Engineered Sharps Injury Protection (SESIP) instruments into impervious sharps discarding containers.
- Attend training programs concerning bloodborne pathogens and following guidelines to limit infection.
- Keep a record of the harm as per the organization’s guidelines.
- Report every instance of needle-stick harm instantly as per the organization’s guidelines.
- Take part in the choosing and analysis of SESIP instruments possessing security characteristics within the confines of the organization when possible
3. Hepatitis B Vaccination – Train your staff on the importance of this vaccine in preventing against Hepatitis B and create a plan for its administration. Almost all employees are subject to this vaccination unless they have a viable reason for declining the vaccine. Make sure all staffs who do not receive the vaccine fill a refusal form and have these kept alongside other exposure control records.
4. After-exposure assessment and monitoring – Conduct a private medical assessment soon after an incident that exposes your staff to Bloodborne pathogens and do a follow-up. Your assessment be comprehensive and include an explanation of the incident that led to the exposure, how the exposed employees were infected among other details per OSHA’s standards.
5. A Blood Pathogen Awareness and Training program – Train you workers on how to report any infection cases and develop a strategy for instant medical diagnosis and action. All employees must undergo training on workplace blood-borne pathogen exposure to increase safety levels. The training should be all-inclusive to ensure you workers are prepared for incidents that could lead to exposure.
6. Keep Records – the Occupations Safety & Health Administration requires employers to keep records related to Bloodborne pathogen training, medical reports, the event that led to the exposure, and needlestick and sharps injury records. How long you’ll need to store these files varies by the type of record. While OSHA expects you to store medical reports for 30 years after a worker exits, you’ll only need to retain training data for three years.
7. Updating your ECP after an exposure. Have one or more of your staffs has been exposed? You can use the opportunity to analyze the effectiveness of your exposure control plan and upgrade it to prevent similar cases in the future.
These seven elements are the fundamentals of an ECP. Without any of them an exposure mitigation strategy may not be as useful as you would like.
Revisit the Occupational Safety and Health Administration’s requirements to ensure whatever you end up with as an ECP is in compliance with the requirements of the law.
Do not operate without an exposure control plan as the consequences can be detrimental. Prevent these cases before they happen with a well-though-out strategy.
Accidents as the Primary Cause of Exposure and The Role of Training in Reducing Risk
A workplace is exposed to Bloodborne pathogens if one or many of the staffs suffer an injury that leads to bleeding and secretion of other potentially infectious body fluids.
Because accidents are the main cause of an exposure, it make sense to always reduce these to a minimum.
And training is the best way to empower your workforce with the knowledge they need to stay safe and protect their colleagues in a workplace.
Employers must appreciate the power of knowledge, and the importance of educating staff on different safety practices.

It is the best way to solve problems due to human-error. You can start by ensuring that each worker knows how to use the tools properly and safely.
This cannot only be achieved by reading the manufacturer’s guidelines. You can have an expert provide hands-on training on safe handling of tools and machines.
And as we’ve learnt from past experiences, practical sessions will make more impact than lectures. This will give them a clear understanding and reduce the possibility of equipment mishandling.
Through this, your workers will also have a clear knowledge about the tools and master how to use them efficiently.
The other part of the training that will yield amazing results is creating awareness about the risk of injuries such as Bloodborne pathogens exposure and how they can be avoided.
Through this, your workers will be well-equipped to protect themselves. Remember; everyone wants to be safe, providing training can make them safer.
You can plan regular training programs led by safety experts, either monthly or yearly, according to the technicality of the tools and machines used in your workplace.
More awareness can be created by adding “safe equipment handling” posters around the workstation. That way, you remind your workers on the safest practices when carrying out their daily duties.
A set of workers should undergo training on machine and tool assessment. They should be able to assess all the parts of the tools and machines, such as rotating and cutting corners, and the joints of cutting edges to ensure that they are firm.
Your workers should also be trained on how to position themselves as they use the equipment to reduce hand injuries. Remind them during training to keep their hands off rotating or cutting parts when operating machines.
Hands must be protected when operating any equipment that uses or requires too much force to manipulate. Training employees on personal safety and safe use of equipment can also reduce cuts and hand lacerations caused by using excessive force on a tool.
You should also ensure that every task is accomplished with the right tool. Using the wrong tool often leads to hand injuries in workplaces. Every tool is built for a specific purpose, using it for jobs other than its intended function can pose injury risks.
Any broken or malfunctioning tool should be repaired or replaced to avoid a shortage of tools in the workstation. Using broken tools also increases the risks of cuts and lacerations. In fact, using faulty equipment is an open danger to the user.
Next, remind your employees of the importance of paying attention in a workstation.
Though accidents are inevitable, past experiences can confirm that attentive and safety-savvy workers are less likely to mishandle a tool or machine; and are, therefore, less likely to get cuts and lacerations while on the job.
An attentive workforce also means more precision and more desirable outcomes. A trained team of staff will easily notice any malfunctioning tool or equipment, or worn out machine parts in good time.
This kind of precaution reduces cases of cuts and lacerations due to faulty equipment ensuring timely repair or replacement.
Alongside reducing injuries, training your workers will also give your company or workshop an amazing growth pace.
Picture a workplace with little to no injuries and cases of cuts and lacerations among employees. It is more productive because every member of the team is safe and sound, and playing their part to push the firm to the next level.
Employee safety should be the employer’s priority. Provide protective gear and repeat safety over and over again until it becomes a culture in your organization.
You don’t want to be the reason an employer loses a finger, suffers an injury or get expose to bloodbore pathogens and infections that will impact the rest of their lives because of a carelessly maintained job site.
Make it your responsibility to reduce the risks of an injury in the working environments. You have to ensure your workplace is safe and in good working condition.
You can also reduce waste products such as glass and metal materials in by implementing a well-though-out disposal plan.
This will ensure proper disposal of sharps that are likely to cause an injury in the site. Training your workers on proper waste disposal will help in keeping the working environment safe.
Sharp wastes must be stored separate from all other forms of waste. Workers can easily get injured when transferring these wastes to dump sites. Do away with sharp tools and wastes as soon as you possible to reduce the risks of injuries in the work zone.
A free navigable and a less cluttered workplace is less prone to hand injuries from sharps than a crowded area where you have to push things aside to make your way.
You also want to ensure breaks in between work sessions to reduce injuries caused by staff burnout.
When people are tired, they are more prone to making mistakes and mishandling tools. Do not overwork your staff. Organize break sessions where drink some water; take some energy foods and check on each other’s wellbeing as you prepare for the next list of tasks.
Use different crews for different shifts if you must work round-the-clock.
Final words
It is the employer’s duty to create an exposure control plan that will protect staff from getting infected with Bloodborne pathogens and give a clear course of action for an exposed individual.
Your exposure control plan must be all-inclusive so you want to carry out a thorough risk assessment analysis to ensure all the dangers are catered for in your final document.
To assess the risks of Bloodborne pathogen exposure, you can analyze the potential risks of accidents (as they are the major cause of exposure) as well as other factors that could lead increases the risks of contracting infections.
An ECP is a legal document so you must prioritize it and ensure you final document is as detailed as possible.
Remember, the document should cover all the risks, the people at risk, steps taken to mitigate the risks and clear course of actions for situations that go out of hand.
And while risk levels may vary from one organization to the other depending on the nature of activities it is involved in, all the workers who might come into contact with potentially infections body fluids while at work should be considered in an ECP.
Lastly, involve your employees when creating an ECP. The best control plans are based on risk assessment and your analysis may not reveal all the risks. Always seek the opinions of your workers when drafting an exposure control strategy.