Online CPR Certification Blog
Guidelines on How to Prevent Workplace Accidents
Date: March 8th, 2024
Injury, disease, death, and property or output loss can all be the outcome of accidents, which are unforeseen occurrences. The Bureau of Labor Statistics reports that in 2020 there were 2.7 million occupational injuries and 4,654 deaths in the United States.
Many got hurt so badly that they couldn’t work anymore. Of course, it should never take a catastrophic event to convince company bosses to alter company policy and prioritize employee and workplace safety.
While it’s impossible to prevent mishaps, there are measures on how to prevent workplace accidents or lessen their likelihood. This article discusses some of the most common causes of workplace accidents and strategies to mitigate various hazards.
But first, what are some of the factors that increase the likelihood of workplace injuries?
Causes of Workplace Accidents
Accidents can be caused by anything from overexertion to the improper handling of dangerous materials. The causes or outcomes of an accident at work might be affected by a wide range of factors, including workplace settings.
Here are some of the common causes of workplace accidents:
Trips and fall
Trips and falls remain a severe workplace issue and are continuously one of the leading causes of injuries. Trip and fall risks increase when surfaces are slippery, workers are in haste, or the weather is terrible.
Tripping over clutter in the workplace is another primary source of injuries. Maintaining a clean and orderly work environment is critical to preventing injuries in the workplace.
Also, there is a high chance of those working at height slipping and falling. In other words, if your job requires you to climb ladders or work in different locations high off the ground, you risk suffering height-related severe injuries if you slip and fall.
Poor Lightening
Inadequate illumination is a common contributor to accidents like slips and falls in the workplace. It’s much more probable that potential problems will escalate into actual emergencies if you can’t see the threats. Offices, storage areas, parking lots, and exterior entrances must have adequate lighting.
Poor lifting
Poor lifting skills are a leading cause of injuries in the workplace. By lifting significant things, you risk injuring your muscles or back. Someone may have a minor injury that heals quickly or a catastrophic one that drastically alters their quality of life.
Accidentally hit by machinery
Falling objects and equipment are a primary cause of fatality in the construction business, and this danger is not limited to that sector.
Inadequate Materials
Employees may be enticed to take unnecessary risks if they need access to the equipment to execute their jobs effectively. Having the proper tools for the job is crucial for maintaining a safe work environment.
Fatigue
Accidents often occur because people are too busy to stop and rest. It’s crucial that workers get enough rest intervals to recover from strenuous manual tasks. Atrophy and fatigue are just two physical problems that can arise from continuous work. The damage done by either of these will likely outweigh the benefits of taking a break.
Dehydration
The effects of dehydration might be just as dire. Heat stroke or heart issues might result from insufficient water on extremely hot summer days. Just drinking enough water (at least eight glasses) every day will keep this from happening.
Stress
Stress can harm a person’s body, mood, and mind and disable or distract even the most dedicated worker. Thus, it is crucial to promote a welcoming and encouraging team atmosphere.
Violent Behavior at Work
Unfortunately, workplace violence has become commonplace. Office politics and other touchy topics are common triggers. Peer mediation and other forms of conflict resolution should be incorporated to lessen the likelihood of violent outbursts.
Overconfidence
Overconfident workers are less likely to take necessary safety measures and are less likely to verify their work. Employees must know that anybody, regardless of their skill level or experience, is vulnerable to an accident at any time.
How to Prevent Workplace Accidents
The ideal working environment would be one where accidents never occur. Unfortunately, accidents can still happen even when we take all necessary precautions.
Here are some of the strategies that may help prevent most workplace injuries and accidents:
Prioritize Workplace Safety
The company’s top priority should always be employee safety. Everyone in the company, from the CEO to the new hire, must know that safety comes first. Develop a comprehensive set of written safety policies and procedures distributed to all employees and prominently displayed in high-traffic areas.
Also, have all employees sign a document attesting to their familiarity with and commitment to the company’s safety standards and protocols.
Review Your Organizational Safety Rules and Procedures
Organizational safety rules and procedures should be reviewed annually and after any workplace accidents. Do they still correspond to the dangers your workers face today? Your safety panel should revise these records whenever there is a modification in the procedure, the introduction of new machinery, or a relocation.
Therefore, it is essential to inform staff of any updates made to safety procedures. Little modifications should be communicated via company-wide email, but significant changes should necessitate new training for all affected employees.
Maintain a Routine of Inspections
Construction, production, shipping, and repairs involve working with potentially lethal machinery. Yet, no employment is risk-free from the possibility of injury.
Therefore, keeping track of maintenance schedules for all your tools and gear is crucial. Verify the security and functionality of all equipment used on the task, from individual hammers to shared workshop machinery.
Continued Training
Along with establishing safety standards in employee guidelines and offering information to recruits, continual learning and instruction are crucial in maintaining a safe workplace.
Employees need thorough training in all facets of their jobs, including proper operation of all equipment and machinery, the recognition of possible hazards, emergency readiness, and dealing with a wide range of emergencies. Better yet, teach your staff CPR and first aid so they can save lives in the event of an emergency.
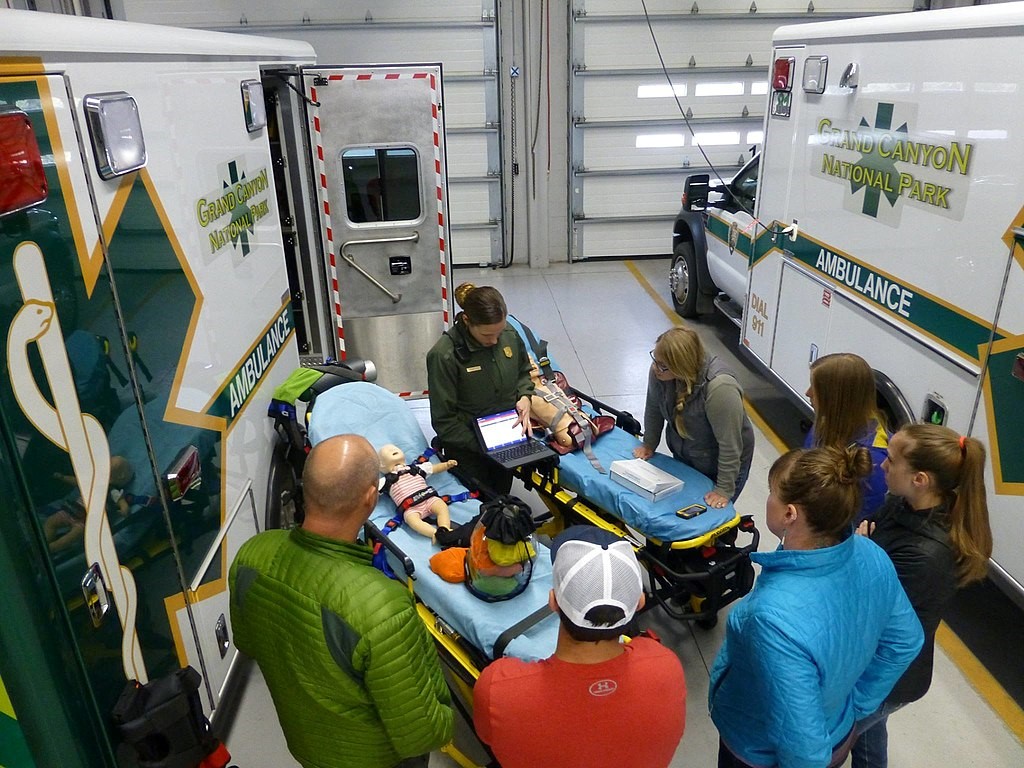
Image alt text: Preventing workplace incidents: Employee safety training for emergency readiness.
Author credits: By Grand Canyon National Park, CC BY 2.0 <https://creativecommons.org/licenses/by/2.0>, via Wikimedia Commons
Manage or Supervise Workers
It is crucial to adequately supervise all personnel, whether working on a building site or office setup. This makes it possible for workers to get answers to their questions from their supervisor quickly and easily.
Uncertain workers may “wing it” without supervision, risking injury, damaged equipment, or extra time spent fixing mistakes. Supervisors can better foster open lines of communication with their staff by receiving training in this area.
Only Get Professionals On Board
Employers must make an effort to find and hire people who are capable of doing the work. The company’s knowledge of maintaining a safe workplace could benefit from any number of available safety certifications.
Before hiring someone claiming to hold a particular certification, it’s essential to research the certification program and their work experience.
Pre-employment physicals are another option for checking the fitness of potential hires for specific jobs. This screening procedure can protect recruits and any other workers who rely on them, and everyone can be assigned work within their physical capabilities.
Recruit Enough Manpower
Understaffing and overburdening existing workers are common causes of accidents. And most workplace accidents are often the result of overworked employees who are too tired or stressed to do their jobs safely because their employers didn’t hire enough people. Hiring temporary or seasonal workers might ease the burden during peak business periods.
Maintain a clean and clutter-free work environment
A cluttered or disorganized workplace is a dangerous one. Ensure that your employees follow all safety procedures, including the simplest ones like keeping the floor clear of tripping hazards caused by computers and power cords.
The proper storage of equipment, the immediate removal of spilled chemicals, and the restriction of dining to designated locations are other essential measures.
Provide protective Gears
To keep workers safe and reduce accidents, PPE (personal protective equipment) must be made available to them at all times and for all tasks where necessary.
Every worker should receive training on the personal protective equipment (PPE) needed to do their jobs safely. That equipment should be maintained and tested often to ensure it performs as expected. Also, ensure you develop or include an active workplace exposure plan to help in cases of infections and pathogens.
Inviting Employee Feedback
Fearing retaliation from their employers, most workers are reluctant to report safety concerns to their superiors. Install a feedback system (suggestion boxes) or reward employees who contribute to a safer workplace.
Conclusion
Various workplaces present different types of accidents. Besides, you can get injured from falling objects, lifting heavy items, and sometimes the wrong use of machinery. Worse, workplace injuries may result from dehydration, fatigue, overconfidence, stress, and workplace violence. Fortunately, organizations can prevent accidents resulting from these factors by providing continued training on hazard identification and risk management and employing enough workforce to avoid fatigue and stress-related injuries. Also, ensure all employees wear protective gear, regularly maintain machinery, conduct routine inspections, and, most importantly, review all the company’s safety regulations or policies.